QUALITY MANAGEMENT
Favoured Prototype Specialist since 1924
Certification:
The A.K.S. Group has been ISO 9001 certified since 1992. Our quality management system ensures the manufacture of quality products that comply with product specifications.
We emphasize that quality management is performed at all stages of the production process. We’re approved by the Danish Working Environment Authorities for marking certified raw materials.
Quality:
Quality monitoring must be planned before the start of production and implemented as an integral part of production, starting with:
Order review:
During the order review, the quality requirements are determined, and the order is added in the computer system. Price and delivery time is confirmed.
Planning:
The work process is planned, and quality checks are inserted and described on route, program, and method cards.
Purchase:
The purchase orders are sent to our approved suppliers. All purchased goods or services are subject to an entry check. The quality of all sub-suppliers is assessed on an ongoing basis.
Production:
Operator checks are carried out on a regular basis. At specified points, coworker checks or intermediate checks are carried out by the quality department. Documentation is provided for each control.
End Inspection:
All items are checked at the exit according to a random sampling plan, or according to customer wishes, e.g., 100% inspection reports can be prepared on request.
Shipping:
All products are securely packaged before shipping. If standard packaging cannot be used, we’ll develop special packaging in collaboration with the customer, to make sure that the product is protected during transport.
Delivery Assurance:
In the case of deliveries from A.K.S., you’ll get the correct product at the agreed time. This is ensured through effective management; from the moment the order is received, through all processes to notification of completion from the quality department.
Services
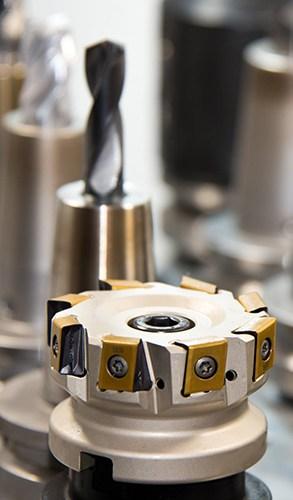
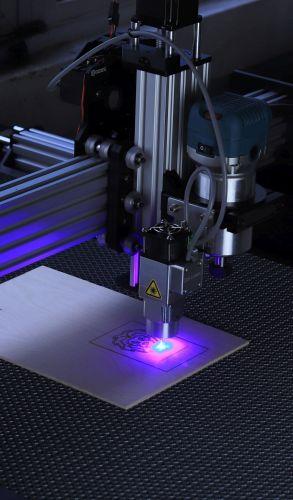